নিটিং মেশিনের সমস্যা ও সমাধান (নতুন পদ্ধতি)

নতুন পদ্ধতি ব্যবহার করে বুনন মেশিনের সমস্যা এবং সমাধান:
সুই ভেঙ্গে যাওয়া:
সমস্যা: বুনন প্রক্রিয়ার সময় ঘন ঘন সূঁচ ভেঙ্গে যায়।
সমাধান: পরিধান বা ক্ষতির লক্ষণ সনাক্ত করে এমন উন্নত সুই পর্যবেক্ষণ ব্যবস্থা প্রয়োগ করুন। দীর্ঘ সুই জীবনের জন্য উন্নত স্থায়িত্ব সহ উপকরণ ব্যবহার করুন।
সুতা খাওয়ানোর সমস্যা:
সমস্যা: অসম সুতা খাওয়ানোর ফলে ফ্যাব্রিকের ত্রুটি দেখা দেয়।
সমাধান: সুনির্দিষ্ট টেনশন নিয়ন্ত্রণের জন্য ইলেকট্রনিক সুতা সেন্সরগুলিকে একীভূত করুন। সামঞ্জস্যপূর্ণ সুতা সরবরাহ নিশ্চিত করতে সার্ভো-চালিত সুতা ফিডার ব্যবহার করুন।
সেলাই গঠনের সমস্যা:
সমস্যা: সেলাই গঠনে অনিয়ম কাপড়ের গুণমানকে প্রভাবিত করে।
সমাধান: রিয়েল-টাইম মনিটরিং এবং সমন্বয় ক্ষমতা সহ কম্পিউটারাইজড নিটিং মেশিন নিয়োগ করুন। সেলাই-দ্বারা-সেলাই নিয়ন্ত্রণের জন্য উন্নত অ্যালগরিদম প্রয়োগ করুন।
ফ্যাব্রিক স্কুইং:
সমস্যা: বুনন প্রক্রিয়া চলাকালীন ফ্যাব্রিক বিকৃতি বা skewing.
সমাধান: ইন্টিগ্রেটেড ফ্যাব্রিক টেনশন কন্ট্রোল সিস্টেম সহ উন্নত বুনন মেশিন ব্যবহার করুন। রিয়েল-টাইমে ফ্যাব্রিক স্কুইং সনাক্ত এবং সংশোধন করতে সেন্সর প্রয়োগ করুন।
প্যাটার্ন মিসলাইনমেন্ট:
সমস্যা: নকশার অসঙ্গতির দিকে নিয়ে যাওয়া প্যাটার্নের মিসলাইনমেন্ট।
সমাধান: সুনির্দিষ্ট প্যাটার্ন নিয়ন্ত্রণ বৈশিষ্ট্য সহ কম্পিউটারাইজড নিটিং মেশিন বেছে নিন। ক্রমাগত প্যাটার্ন পর্যবেক্ষণ এবং সংশোধনের জন্য উচ্চ-রেজোলিউশন ক্যামেরা ব্যবহার করুন।
মেশিন ডাউনটাইম:
সমস্যা: রক্ষণাবেক্ষণ বা প্রযুক্তিগত সমস্যার কারণে ঘন ঘন ডাউনটাইম।
সমাধান: মেশিনের স্বাস্থ্য নিরীক্ষণ করতে IoT সেন্সর ব্যবহার করে ভবিষ্যদ্বাণীমূলক রক্ষণাবেক্ষণ প্রয়োগ করুন। ডাউনটাইম হওয়ার আগে সম্ভাব্য সমস্যাগুলি সনাক্ত করতে স্ব-নির্ণয়ের সিস্টেম ব্যবহার করুন।
শব্দ এবং কম্পন:
সমস্যা: মেশিন অপারেশনের সময় অত্যধিক শব্দ এবং কম্পন।
সমাধান: মেশিন নির্মাণে কম্পন-স্যাঁতসেঁতে উপকরণ এবং প্রযুক্তি ব্যবহার করুন। শব্দ কমানোর ব্যবস্থা প্রয়োগ করুন, যেমন অ্যাকোস্টিক ঘের এবং উন্নত স্যাঁতসেঁতে সিস্টেম।
শক্তি খরচ:
সমস্যা: ঐতিহ্যবাহী বুনন মেশিনের উচ্চ শক্তি খরচ।
সমাধান: উন্নত মোটর প্রযুক্তি সহ শক্তি-দক্ষ বুনন মেশিনে বিনিয়োগ করুন। হ্রাসের সময় শক্তি পুনরুদ্ধার করতে পুনর্জন্মমূলক ব্রেকিং সিস্টেম ব্যবহার করুন।
উপাদানের অপচয়:
সমস্যা: বুনন প্রক্রিয়া উচ্চ উপাদান অপচয়.
সমাধান: বুদ্ধিমান কাটিং সিস্টেম প্রয়োগ করুন যা উপাদান ব্যবহারকে অপ্টিমাইজ করে। ফ্যাব্রিকের অবশিষ্টাংশ কমাতে এবং সামগ্রিক বর্জ্য কমাতে উন্নত অ্যালগরিদম ব্যবহার করুন।
জটিল প্যাটার্ন এক্সিকিউশন:
সমস্যা: জটিল এবং জটিল বুনন প্যাটার্ন কার্যকর করতে অসুবিধা।
সমাধান: প্যাটার্ন তৈরির জন্য কম্পিউটার-এডেড ডিজাইন (CAD) সফ্টওয়্যার ব্যবহার করুন। উচ্চ-স্তরের প্রোগ্রামযোগ্যতা এবং ডিজিটাল ডিজাইন ফাইলগুলির সাথে সামঞ্জস্যপূর্ণ বুনন মেশিনগুলি বেছে নিন।
স্বয়ংক্রিয় রঙ পরিবর্তন:
সমস্যা: ম্যানুয়াল রঙ পরিবর্তনের ফলে উৎপাদন বিলম্ব হয়।
সমাধান: স্বয়ংক্রিয় রঙ-পরিবর্তন সিস্টেম সহ বুনন মেশিনে বিনিয়োগ করুন। নির্বিঘ্ন এবং দ্রুত রঙ পরিবর্তনের জন্য রঙ সেন্সর এবং প্রোগ্রামেবল লজিক কন্ট্রোলার (PLCs) প্রয়োগ করুন।
নতুন পদ্ধতি ব্যবহার করে বুনন মেশিনের চ্যালেঞ্জ মোকাবেলায় উত্পাদন প্রক্রিয়ায় দক্ষতা, নির্ভুলতা এবং সামগ্রিক কর্মক্ষমতা বাড়ানোর জন্য অত্যাধুনিক প্রযুক্তি, অটোমেশন এবং বুদ্ধিমান সিস্টেমগুলি অন্তর্ভুক্ত করা জড়িত। সফল বাস্তবায়নের জন্য এই উন্নত বৈশিষ্ট্যগুলি ব্যবহার করার বিষয়ে অপারেটরদের নিয়মিত প্রশিক্ষণ অপরিহার্য।

এই পোস্টের মধ্যে নিটিং ফল্টগুলো সম্পর্কে আলোচনা করব।
Table of Contents
নিটিং ফল্টগুলো (Knitting Faults)
- ইয়ার্ন ডাস্ট (Yarn Dust)
- সেট – আপ (Set – Up)
- লুপ মার্ক (Loop Mark)
- নিডেল কাট (Needle Cut)
- অয়েল স্পট (Oil Spot)
- মিক্স ইয়ার্ন (Mix Yarn)
- হোল (Hole)
- লাইক্রা আউট (Lycra Out)
- ইয়ার্ন মিসিং (Yarn Missing)
- স্টার ফল্ট (Star Fault)
ইয়ার্ন ডাস্ট (Yarn Dust)

কারণ :-
নিটিং মেশিন ভালোভাবে পরিষ্কার না করার ফলে এবং নিটিং মেশিন ভালোভাবে পরিচালনা করা হলে ইয়ার্ন ডাস্ট সমস্যাটি দেখা দেয়।
ফেব্রিকে ইয়ার্ন ডাস্ট থাকলে ডাইংয়ে সমস্যা হবে এবং কস্টিং বেড়ে যাবে।
প্রতিকার :-
নিটিং মেশিন ভালোভাবে পরিষ্কার করতে হবে। মেশিন ভালোভাবে পরিচালনা করতে হবে এবং ওয়াশিং ফার্স্টনেস বাড়ালে এই ফল্ট রোধ করা সম্ভব।
সেট – আপ (Set – Up)

কারণ :-
নেডেল ব্রেক এবং ইয়ার্ন ব্রেক এর কারনে এই সমস্যাটি হয়ে থাকে।
প্রতিকার :-
নিটিং মেশিন চলাকালীন অপারেটরকে সতর্ক থাকতে হবে, যেন নেডেল ব্রেক এবং ইয়ার্ন ব্রেক হলে সাথে সাথে সঠিক পদক্ষেপ নিতে পারে।
লুপ মার্ক (Loop Mark)

কারণ :-
নিডেলের সমস্যা থাকলে এবং নিডেল যদি ঠিক মত কাজ না করে তাহলে এই সমস্যা দেখা দেয়।
প্রতিকার :-
পুরাতন নিডেল পরিবর্তন করে নতুন নিডেল লাগাতে হবে এবং নিডেল হূক পরিষ্কার রাখতে হবে।
নিডেল কাট (Needle Cut)

কারণ :-
ফেব্রিক নিটিং এর সময় ইয়ার্ন ফিডার এবং নিডেল সঠিকভাবে সেটিং না করা হলে ফেব্রিক এ নিডেল কাট দেখা দিতে পারে।
প্রতিকার :-
ইয়ার্ন ফিডার এবং নিডেল মাঝখানে নির্দিষ্ট পরিমাণ ফাঁকা রাখতে হবে। ভালোভাবে ইয়ার্ন ফিডার এবং নিডেল সেটিং করতে হবে।
অয়েল স্পট (Oil Spot)

কারণ :-
নিটিং মেশিন ফ্রি ভাবে চলার জন্য অয়েল ব্যবহার করা হয়, সেই অয়েল লিক করে ফেব্রিকে অয়েল স্পট তৈরি করতে পারে।
প্রতিকার :-
অয়েল যেন লিক না করে সেদিকে অবশ্যই অপারেটরকে খেয়াল রাখতে হবে।
মিক্স ইয়ার্ন (Mix Yarn)

কারণ :-
নিটিং এর সময় অপারেটরের অসতর্কতার ফলে অন্য কোন ইয়ার্ন মিক্স হয়ে যেতে পারে।
প্রতিকার :-
নিটিং করার সময় অপারেটরকে সতর্ক থাকতে হবে।
হোল (Hole)
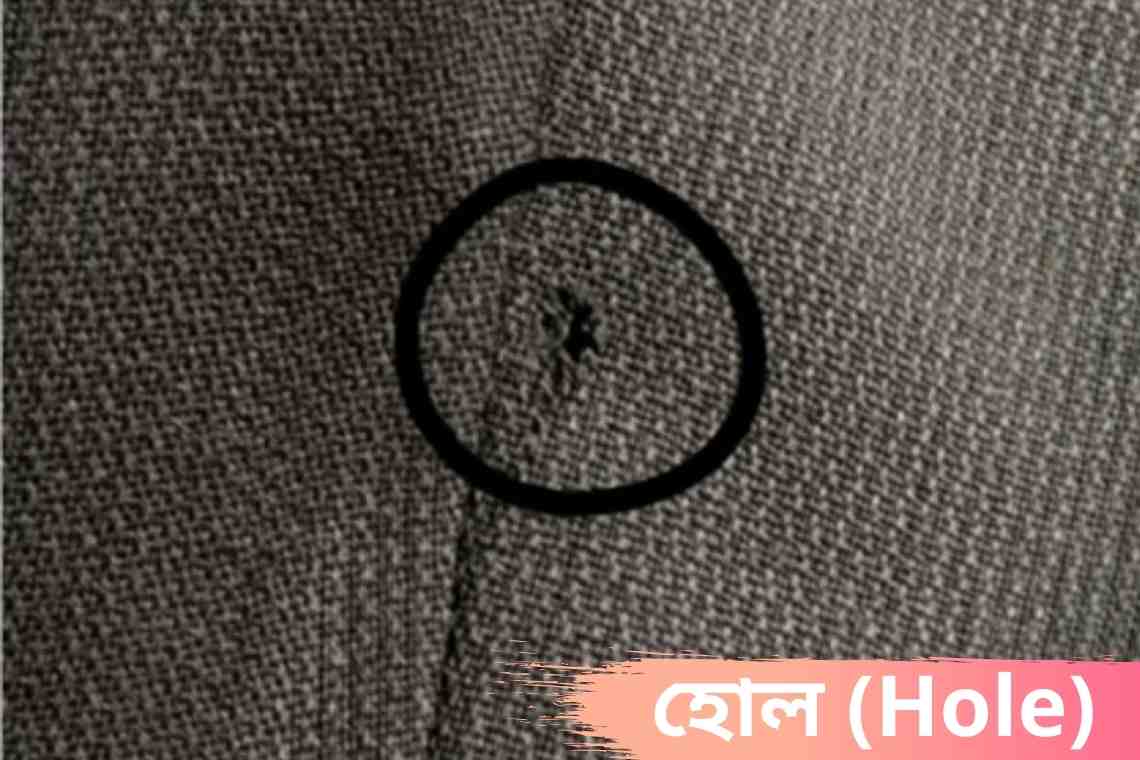
কারণ :-
ইয়ার্ন ফিডার যথাযথভাবে সেটিং না হলে অথবা ইয়ার্ন কাউন্ট ঠিক না হলে মিটিং কৃত ফেব্রিকে হোল দেখা দিতে পারে।
প্রতিকার :-
ইয়ার্ন ফিডার সঠিকভাবে সেট করতে হবে এবং ইয়ার্ন কাউন্ট সঠিক রাখতে হবে।
লাইক্রা আউট (Lycra Out)

কারণ :-
রোলার ব্লক এবং নিডেল সঠিকভাবে কাজ না করলে সাধারণত লাইক্রা আউট সমস্যাটি দেখা দেয়।
প্রতিকার :-
অপারেটরকে সচেতন থাকতে হবে।
ইয়ার্ন মিসিং (Yarn Missing)
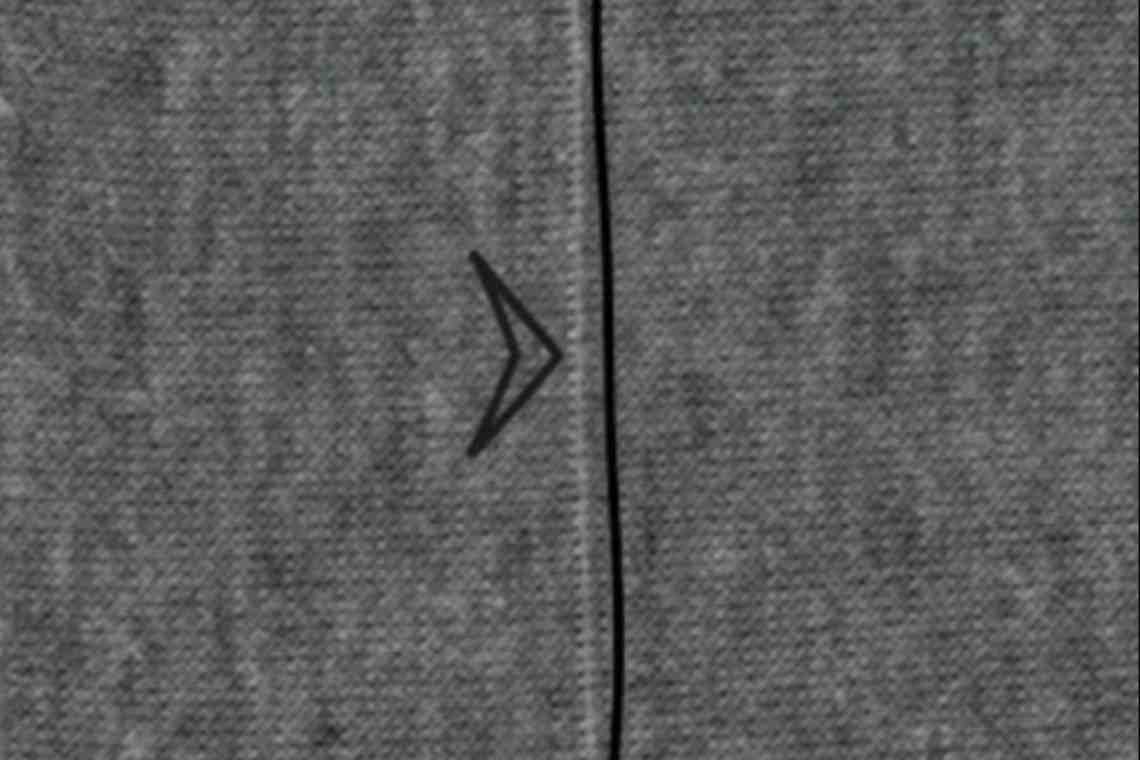
কারণ :-
নিডেল সঠিকভাবে কাজ না করলে, গোড়া থেকে ইয়ার্ন ছিড়ে গেলে।
প্রতিকার :-
নিডেল সঠিকভাবে কাজ করছে কিনা তার দিকে খেয়াল রাখতে হবে এবং অপারেটরকে সতর্ক থাকতে হবে।
স্টার ফল্ট (Star Fault)
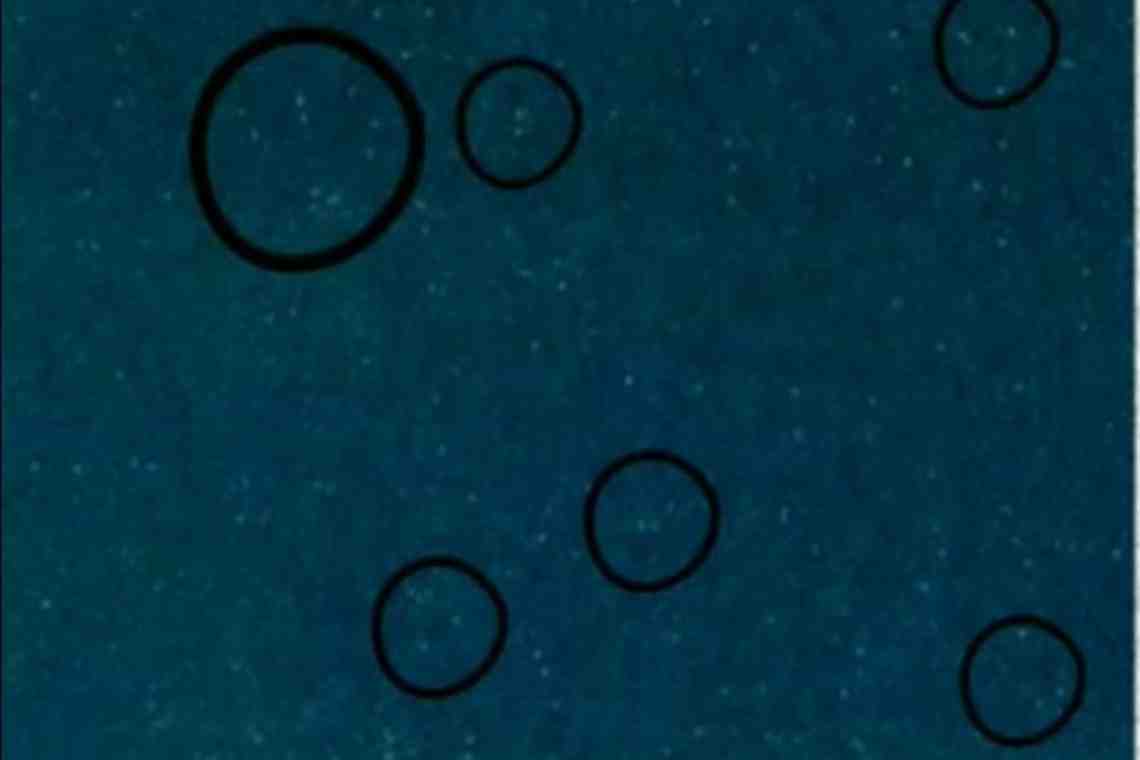
কারণ :-
নিটিং করার সময় নিটিং মেশিনের এমসি সিলিন্ডারের আরপিএম হাই থাকলে ফেব্রিকে স্টার ফল্ট দেখা দিতে পারে।
প্রতিকার :-
অপারেটরকে অবশ্যই পারদর্শী এবং সতর্ক হতে হবে।